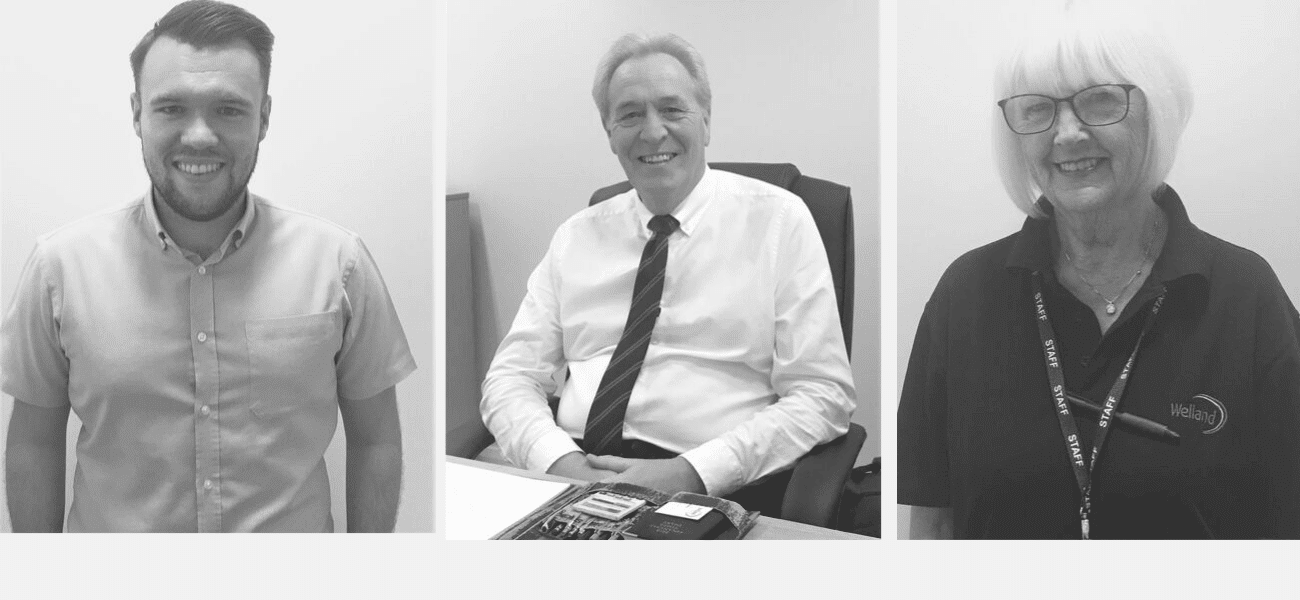
30 Years of Welland Medical
In 1988 Welland Medical’s journey as a British manufacturer of stoma care appliances commenced. 30 years on and Welland Medical is now firmly established as one of the leading ostomy brands in the UK and worldwide. Renowned for manufacturing ground breaking stoma care solutions, Welland Medical has come on leaps and bounds from its humble beginnings in Billingshurst, West Sussex.
Growing from a team of 15 to a workforce of over 200 during the 30-year transition from a small local company to a global manufacturer, Chris Primett, Managing Director, comments: “Our workforce is at the heart of our success and they are, and will continue to be, our greatest asset. Each specialising in fields including Production and Operations, Engineering, Sales and Marketing, Research and Development, Finance, Human Resources and Regulatory Affairs, our talented workforce is responsible for overseeing the design, development and manufacture of the company’s innovative stoma care solutions for people who have had bowel or bladder surgery due to cancer or disease”.
In a time where many workers spend five years or less in every job1, Welland Medical’s choice to place staff at the heart of the business has been rewarded with more than 30% of the workforce celebrating over ten years’ service with the company. Longest serving employee Helen Gilbert, HR Manager, has been with Welland Medical since the beginning. Reflecting on the last 30 years Helen commented: “Being involved in this incredible journey has been a truly inspiring experience and one which I am very proud to have been part of”.
The transition from a small office in Billingshurst to a purpose built state of the art research, development and manufacturing facility located in Manor Royal, Crawley, has been a journey enjoyed by all. Forward thinking, commitment to innovation and continuous improvement has seen Welland Medical outgrow 8 manufacturing sites in a bid to keep abreast of the latest technological advancements in design and automated manufacturing. Longest serving company Director, David Margetts, has experienced some incredible developments over the years. Joining in 1999 as Operations Manager and the Board of Directors as Operations Director in 2004, David commented: “Automation of our processes has catapulted the Manufacturing department on to another level. Who would have thought when we were making pouches by hand that we would eventually utilise robotics and even laser technology in the delivery of our products. That being said our people and their dedication is still the key to our continued success”.
Witness to so many of these developments are long-standing staff members Ian Lees, Tracey Berry, Nicola Howard and Jill Jarosinski, who have each celebrated over 20 years’ service. From the introduction of the first automated machine, 24 hour manufacturing to meet an ever-increasing demand and a continuously growing team and product portfolio to keep up with, their stories offer a glimpse into the company’s history and provide an insight in to how these developments have allowed Welland Medical to become the global player that it is today.
Joining in 1994, Ian, an Operative in the Hydrocolloid department, witnessed the development of Welland Medical’s signature hydrocolloid formulation, a natural, skin friendly adhesive that has been protecting ostomates skin for three decades. With automated technology now streamlining what was predominately a manual process when Ian joined, the department has transformed, with Ian commenting: “The technology has expanded way beyond what I ever thought was possible”. Going on to discuss why he still enjoys his role after 23 years, Ian said: “We are always looking forward to find a better way of doing things, it’s exciting. The introduction of Manuka honey in to the hydrocolloid formulation to produce our Aurum® range of products is something I never imagined. I can’t wait to see what we do next!”
Nicola and Jill, Production Operatives, have become firm friends over the years, reminiscing over Christmas parties and corporate days out it is clear that the pair hold fond memories of their time at Welland Medical, with Jill commenting: “After 27 years I still come in to work with a smile on my face”. Since welcoming the first automated machine in 1993, the days when Nicola and Jill were making products by hand, using time-consuming intricate processes are distant memories. As the number of new machines increased over time, each offering an automated alternative to a previously manual task, production levels have soared, with the manufacture of stoma pouches increasing by over 95% in the last ten years alone. Reflecting on the introduction of new technology Nicola commented: “I have never looked back. Without the new machines we would never be able to keep up with the increasing demand, our hands just wouldn’t be able to work quickly enough”.
Tracey Berry, Production Operative, explains why she still experiences the same sense of satisfaction from producing a Welland Medical ostomy pouch today, as she did 27 years ago when she joined the company: “After 30 years our products continue to help ostomates around the world. Knowing that I have played a part in this gives me a great sense of satisfaction”.
After an incredible 30-year journey, the focus turns towards the future. Working in partnership with Crawley College to offer an apprenticeship scheme for employees, Chris Primett commented: “This scheme offers us the opportunity to invest in our future workforce and provides us with the unique ability to be able to ensure that the skills our apprentices develop are perfectly matched to our future needs”.
Since the introduction of the scheme in 2008, Welland Medical has trained seven apprentices who have gone on to further their careers in departments including Quality Assurance, Engineering and Finance. Bradley Dickinson, Supply Chain Co-Ordinator, is one of these employees. Starting his two-year Production Operative apprenticeship in 2013, Bradley has gone on to enjoy a role within the Purchasing department. Discussing his experience, Bradley comments: “My apprenticeship has opened the door to my future career. I am now in a role I enjoy, which I would have never discovered without the apprenticeship programme. Putting in the hard work has paid off and knowing that the skills I have learnt along the way are helping to benefit both my department and the company’s future makes it even more rewarding.”
With sales increasing, new products in the pipeline and more machinery on order the future looks exciting for Welland Medical.
References
1. Doyle, A. 24.01.2018. The Balance Careers. How Often do People Change Jobs? [Online] Available at: www.thebalancecareers.com/how-often-do-people-change-jobs-2060467 [accessed 01.08.2018]